Tout le monde en convient : les camping-cars à carrosserie monocoque surclassent dans tous les domaines – isolation, étanchéité, durabilité … – les carrosseries classiques réalisées par assemblage de panneaux. Mais alors, qu’est-ce qui explique que ce type de carrosserie dite autoportante reste l’apanage d’une poignée de constructeurs en Europe ? Éléments de réponse.
Une fabrication inspirée du bateau
Contrairement aux carrosseries à panneaux assemblés, les plus courantes sur le marché, les carrosseries monocoques sont conçues d’un seul tenant, à partir d’un moule. Elles sont ainsi autoportantes. C’est-à-dire qu’elles n’ont pas besoin d’ossature en bois ou en acier pour se tenir. Ce process de construction – courant dans l’industrie nautique (pour les voiliers) et même dans le monde de la Formule 1 – a pour lui un grand nombre d’avantages. En voici les principaux :
- Étanchéité maximale car pas de soudure et donc pas d’infiltration ni de corrosion
- Isolation thermique et acoustique optimale car pas de joints, ni de pièce métallique conductrice, et donc pas de pont thermique
- Condensation minimale à l’intérieur
- Meilleure résistance de la cellule aux torsions liées aux vibrations et chocs de la route
- Rigidité accrue de l’ensemble de la carrosserie, d’où une sécurité renforcée en cas d’accident
- Design extérieur plus abouti grâce à la possibilité de proposer des formes complexes et d’intégrer à fleur de carrosserie certains éléments (portes de coffres et soute, vitrages, trappes…)
- Réparabilité plus grande (pas de besoin de remplacer un panneau en cas de choc important)
- Gain de poids
On l’aura compris : les carrosseries monocoques cumulent les atouts par rapport aux cellules fabriquées de manière conventionnelle. Mais alors, pourquoi restent-elles circonscrites à quelques marques haut de gamme ?
Des moules onéreux
Pour le savoir, nous avons interrogé la référence française de ce type de construction : 3C Cartier. Basée dans l’agglomération lyonnaise, l’entreprise fabrique des carrosseries de camping-cars et véhicules spéciaux – notamment pour l’Armée de Terre – depuis 1982. Ses cellules monoblocs représentent aujourd’hui ce qui se fait de mieux dans le secteur.
À la manière d’un atelier de haute couture, chaque « peau » est ici réalisée sur-mesure, à partir d’un grand moule. L’atelier en compte sept différents, tous fabriqués maison. Chaque moule coûte ici entre … 300 000 € et 500 000€ !
Un travail d’orfèvre
« Il faut comprendre qu’une carrosserie monocoque de camping-car nous demande 700 à 800 heures de travail (hors temps de séchage). Et même jusqu’à 2000 heures pour une caisse de camion d’expédition, pose François-Xavier Fousse, dirigeant de 3C Cartier. Un temps de travail sans commune mesure avec celui d’une carrosserie traditionnelle par assemblage de panneaux.
« Nous créons la carrosserie dans des moules de largeurs déterminées selon le porteur, mais modulable en longueur selon le choix du client, précise le patron de 3C Cartier. Pour un rendu parfaitement homogène, l’injection des différentes stratifications de la carrosserie dans le moule est effectuée à la main. Et chaque porte, trappe ou fenêtre est positionné au centimètre près ».
Aussi, contrairement à une cellule classique, où l’on construit l’aménagement intérieur avant de monter les murs, tous les équipements doivent ici passer par la porte et les ouvrants. Ce qui rend la tâche plus longue et complexe.
3C Cartier : des monocoques pas comme les autres
Les cellules monocoques de 3C Cartier cultivent leurs singularités. « Contrairement à d’autres, nos coques sortent du moule entièrement finies. C’est-à-dire qu’elles intègrent déjà l’isolation, le plancher ou les réservoirs, souligne François-Xavier Fousse. Elles sont à ce titre totalement étanches et sans pont thermique. Avec une rigidité incomparable ». A l’inverse, sur les cellules monocoques Wingamm, Atlantis Camper ou La Strada par exemple, le plancher n’est pas intégré à la coque, mais rapporté et boulonné dans un second temps.
En vrai spécialiste des véhicules off-road, 3C Cartier a par ailleurs développé son propre système de fixation des cellules sur des châssis 4×4. Son système breveté fait appel à un procédé élastique qui permet d’absorber les vibrations et d’éviter les torsions de la cellule (300% d’élasticité et résistance de 150 tonnes à l’arrachement !). Peu de concurrents sont ici capables de s’aventurer sur ce terrain des cellules monoblocs sur châssis 4×4. « Certains ont essayé, mais ils n’avaient pas le savoir-faire » sourit François-Xavier. On peut tout de même citer ici, parmi quelques autres, le spécialiste allemand Darc Expedition, dont les cellules monoblocs sont greffés aux châssis Iveco Daily 4×4 avec des suspensions spécifiques.
Des composants haut de gamme
Au-delà de la fabrication des moules et du temps imparti pour réaliser la cellule monocoque, la qualité des composants explique également le coût plus élevé de ce type de fabrication. Chez 3C Cartier, la carrosserie est désormais composée d’une double peau de vinylester, un « matériau trois fois plus résistant que le polyester », entre lesquelles est insérée de la mousse de polyuréthane (35 mm dans les parois, 45 mm dans le plancher). Unique et sans comparaison avec tout ce que l’on peut voir ailleurs.
A la manière de constructeurs aéronautiques, l’entreprise lyonnaise utilise par ailleurs des matériaux haut de gamme comme le kevlar ou la fibre de carbone pour certaines zones stratégiques. « Pour le carbone, nous en mettons au niveau de la cabine, des passages de roues et de l’arrière du véhicule afin d’apporter de la rigidité et de bloquer les vibrations mécaniques », détaille le dirigeant de 3C Cartier.
Du carbone, on en trouve aussi directement dans la composition des carrosseries. Comme chez Atlantis Camper. Ce jeune fabricant italien spécialiste de la monocoque a présenté cette année au Caravan Salon de Düsseldorf le Carbon 595 : un camping-car haut de gamme, avec une carrosserie à double-peau en fibre de carbone. Un matériau robuste et qui permet d’alléger la cellule de 30% (environ 100 kg), mais qui alourdit la facture finale de plus de 50.000 € par rapport au même modèle avec carrosserie polyester ! Cela fait cher le kilo gagné…
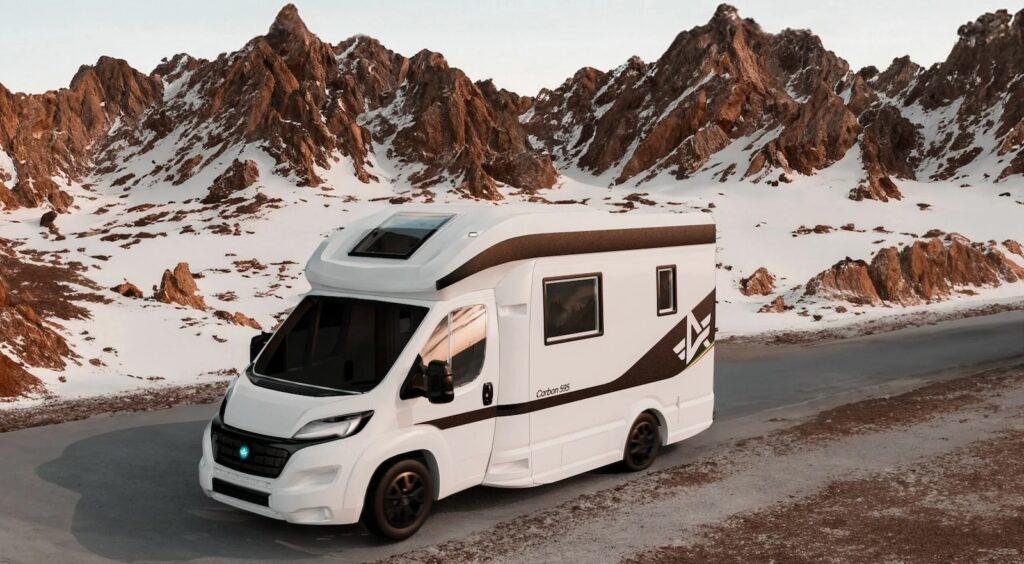
Pour contrer l’argument de la cherté de ses camping-cars monocoques, la marque fondée en 2021 aime à rappeler que ses modèles sont conçus pour durer. Et qu’ils garderont en conséquence une très bonne valeur de revente. Un point à avoir en tête, pour tous les camping-cars à carrosserie monocoque.
Des process difficilement industrialisables
Un ancien responsable de marque française de camping-car, qui préfère garder l’anonymat, nous confirme que les process de fabrication d’une cellule monocoque sont compliqués à industrialiser.
« Nous avons étudié à l’époque le sujet sous tous les angles. Mais le cahier des charges est strictement impossible à tenir pour un industriel. La technologie monobloc implique beaucoup d’opérations manuelles (démoulage, peinture, reprise des plans de joint, etc.), ce qui multiplie le prix par trois ou quatre par rapport à une cellule classique, explique-t-il, avant d’ajouter. Le poids était aussi à l’époque un vrai sujet. Même sur des véhicules de 6 mètres, la limite des 3,5T était difficile à tenir ». Un dernier argument qui ne semble plus d’actualité : la plupart des spécialistes vantent le poids plus léger de leur monocoque par rapport à une carrosserie classique.
La monocoque, certains fabricants industriels s’y sont pourtant essayés. A l’image de Le Voyageur, qui a commercialisé à partir de 1991 des camping-cars monocoques sous les noms de gammes SV (sur Renault, Peugeot ou Citroën), puis VX (Mercedes). La production est alors limitée à quelques unités seulement. Mais les coûts de fabrication et de production sont tels que les deux gammes sont arrêtées en 1993, juste avant le rachat de la marque l’année suivante.
L’exemple italien
En Italie, la fabrication de camping-cars monocoques est historiquement plus répandue qu’ailleurs. Un héritage du savoir-faire acquis dans la construction de bateaux ? Quoi qu’il en soit, plusieurs constructeurs ont fait le pari de produire en petites séries ce type de camping-cars. Le plus connu d’entre eux est évidemment Wingamm. La marque dispose aujourd’hui à son catalogue de 8 modèles (5 gabarits de longueur). Mais elle le reconnaît également : il reste difficile d’industrialiser les tâches. « Une cellule monocoque nécessite 10 fois plus de temps à construire qu’un camping-car traditionnel à panneaux assemblés », assure-t-elle, citant elle-aussi la stratification de la carrosserie à la main.
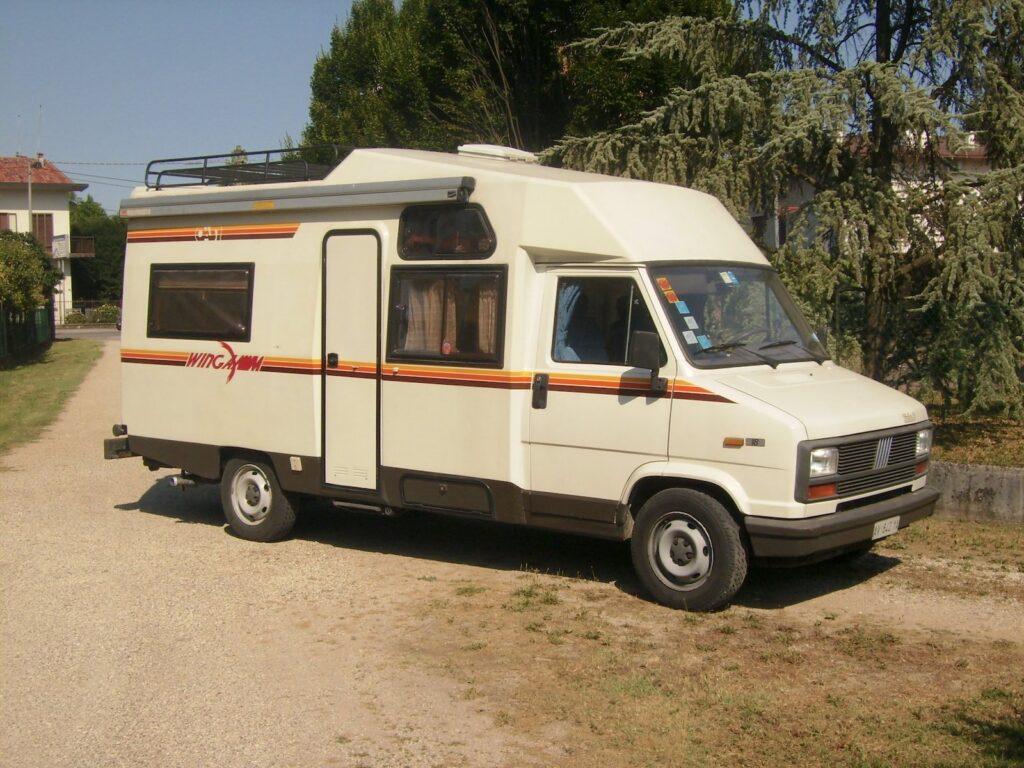
Même constat chez le voisin Atlantis Camper, qui propose lui 3 modèles de camping-cars, de longueurs distinctes, correspondants chacun à un moule. « Si nous pouvons optimiser un peu la fabrication en faisant du volume, le process de stratification (fibre de polyester / PVC / gel-coat) reste manuel et requiert des techniciens hautement spécialisés » , témoigne Marco Soliman, responsable marketing de la marque.
Des solutions alternatives moins complexes
L’industrie du camping-car a donc, pour des raisons de coûts essentiellement, massivement adopté la fabrication de carrosserie par assemblage de panneaux. Toutefois, certaines marques ont emprunté des voies alternatives.
C’est le cas par exemple du Français Le Voyageur (groupe Pilote) qui a été le premier à proposer, dès 1980, un toit monobloc bombé à recouvrement. A la manière d’un couvercle de boite, ce dernier enveloppe les montants hauts des parois. Ce qui évite les rétentions d’eau et les risques d’infiltration.
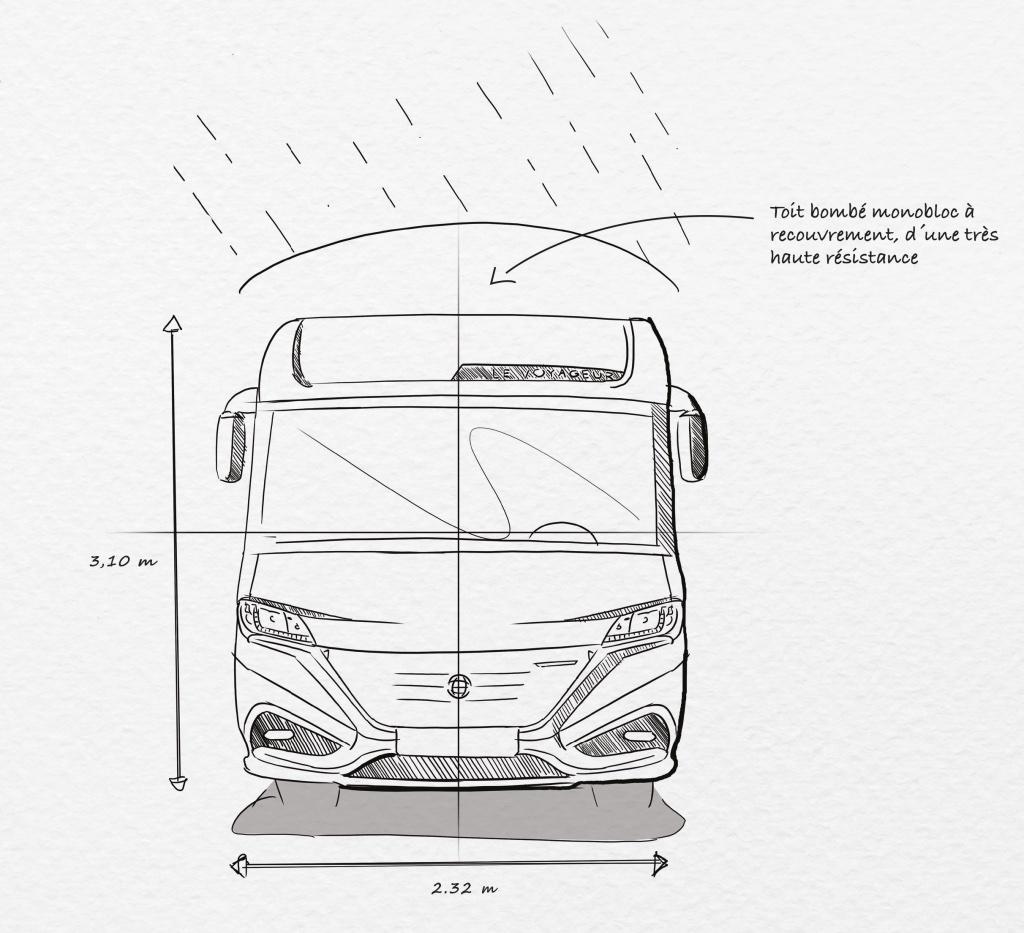
Fleurette et Florium (groupe Rapido) produiront également plus tard leur propre toit à recouvrement. Avec ce procédé, la construction d’un panneau sandwich nécessite à lui-seul près d’une semaine de travail.
D’autres encore ont fait le choix d’avoir recours à des faces avant (Pilote Galaxy par exemple) ou arrière (Notin Excel) monoblocs. Si ces solutions de pièces monoblocs n’ont plus grand chose à voir avec une véritable carrosserie monocoque, elle ont le mérite d’offrir une bonne étanchéité sur les parties concernées et … un coût global plus maîtrisé.
Les commentaires sont fermés.